REFRACTORY
Powermaster >Home > Technical guide > Refractory
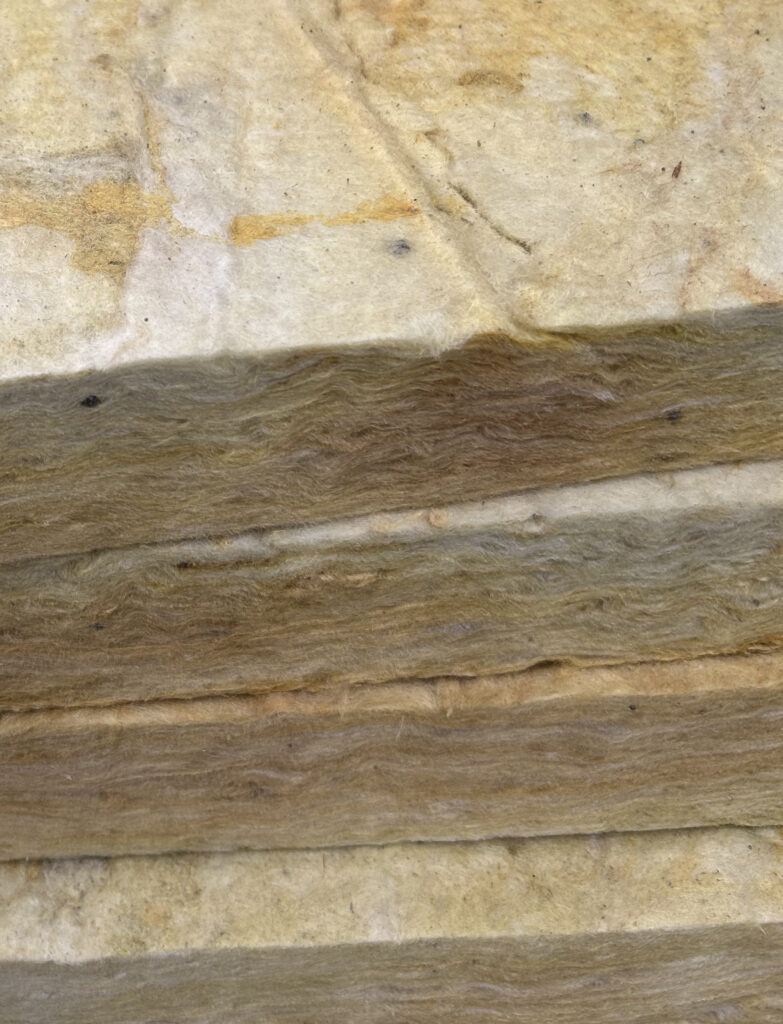
Refractory material is the most fragile material used in boiler design. It breaks easily and repairing or replacing the refractory parts is quite expensive, often rendering the boiler out of commission for long periods of time.
Old boiler designs used refractory material (cement or brick) to isolate those areas of the boiler in which the flame or combustion gases came into direct contact with steel that did not have water on the other side to cool it down.
In old fire tube boilers, refractory material was most commonly used in the gas turnaround chamber and in the doors. Using such large quantities and complex geometries of refractory materials made these areas very fragile – especially the refractory bridge, which is the part of the boiler that separates the gases of the second and third passes.
Modern boiler designs minimize the use of refractory material which, in turn, increases the reliability and efficiency of the boiler and decreases maintenance costs and requirements.
A modern, horizontal fire tube boiler with 80 or more horsepower does not require a refractory framework as its steel turnaround chamber is now cooled by water (the Wet-Back design; see Technical Guide: Wet-Back) and the front and back doors are now made with stainless steel sheets backed with mineral wool.
All Powermaster fire tube boilers with 80 or more horsepower are manufactured with a Wet-Back design; none include refractory material in the front or back doors. The only refractory material contained is found in the Wet-Back manhole and in the refractory nozzle of the burner. This ensures a more efficient and reliable boiler with lower maintenance costs.